Manitou entame l’automatisation de sa supply chain avec Mecalux
Le spécialiste des engins de manutention, Manitou, vient d’inaugurer son premier grand projet de mécanisation d’entrepôt à Ancenis, confié à Mecalux. Ce nouvel équipement va apporter des gains de productivité très importants à sa BU Spare Parts qui livre chaque année environ deux millions de lignes, soit un peu plus de 12 millions de pièces.

Un peu plus de six mois après avoir pris en main cette ligne automatisée installée par Mecalux dans son entrepôt d’Ancenis, la division après-vente pièces détachées est prête à faire décoller les gains de productivité escomptés. « Nous cherchions une capacité minimum de 400 à 500 lignes à l’heure. Nous l’avons atteinte aujourd’hui assez facilement. Nous sommes plutôt confiants sur le fait de pouvoir augmenter cette cadence », anticipe Laurent Maunoir, directeur supply chain après-vente et pièces détachées.
20 % des références sur 5 % de la surface
L’installation de Mecalux compte 20 000 bacs, 46 navettes et cinq ascenseurs avec une emprise au sol de 900 m2 sur une dizaine de mètres de hauteur. Elle permet de stocker 16 000 références sur un total de 80 000 références dans l’entrepôt. « Nous arrivons aujourd’hui à stocker 20 % de nos références sur 5 % de la surface », explique Laurent Maunoir.
L’entrepôt d’Ancenis est l’un des huit que compte la business unit après-vente et pièces détachées en France, en Italie, en Inde, aux Etats-Unis, au Brésil, en Russie, en Afrique du Sud et à Singapour, tous opérés par des collaborateurs du groupe. Étant donné l’importance qu’y revêt la fonction supply chain, pas étonnant que Manitou commence à investir dans la mécanisation de sa logistique en commençant par cette BU qui représente 12 à 13 % du 1,9 milliard d’euros de chiffre d’affaires du groupe (2021).
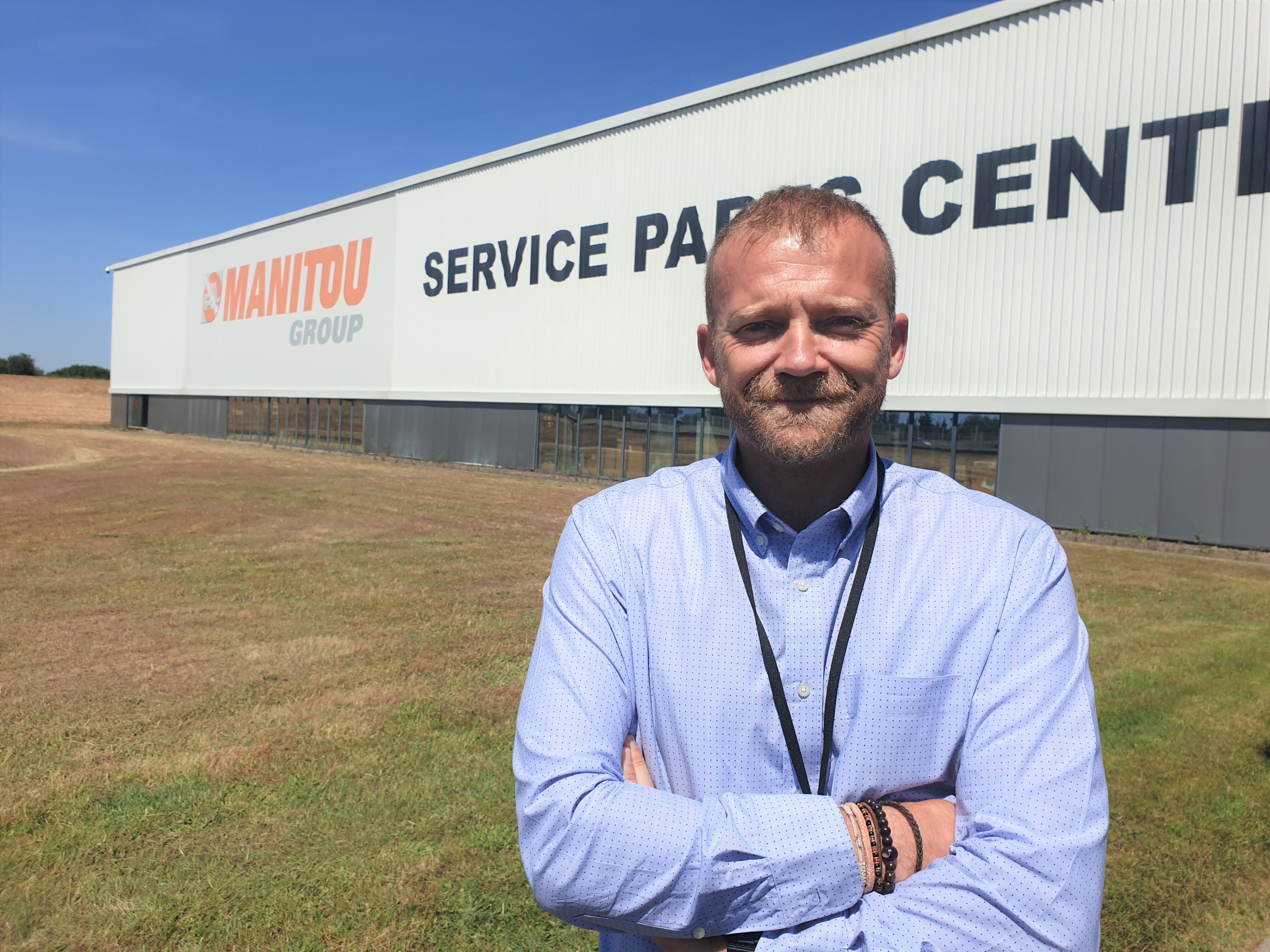
La supply chain dans la pièce détachée est plus considérée comme un avantage concurrentiel que ressentie comme un centre de coûts
« Tout ce qui se passe après que le client a reçu sa machine, c’est ce qui nous garantit qu’il sera satisfait et qu’il commandera d’autres machines à l’avenir. La supply chain dans la pièce détachée est plus considérée comme un avantage concurrentiel que ressentie comme un centre de coûts », assure Laurent Maunoir. Sur les quelque 350 collaborateurs que compte la BU pièces après-vente pièces détachées, les deux-tiers sont rattachées à la supply chain.
Des références et des besoins de stockage en hausse
Focalisée sur le taux de service client, la direction supply chain concentre son action sur deux priorités : la disponibilité des pièces et la capacité des entrepôts à distribuer en temps et en heure, deux sujets sur lesquels l’automatisation de l’entrepôt doit apporter un ROI rapide dans un contexte d’accroissement du nombre de de références à stocker, d’une part, et de besoin accru de réactivité d’autre part.
Nos entrepôts de distribution ne sont pas capables de stocker la totalité du référentiel. Ils doivent donc être hyper réactifs
« Nous avons un très large catalogue de machines et un vaste référentiel de pièces détachées ; tous nos entrepôts de distribution ne sont pas capables de stocker la totalité du référentiel. Ils doivent donc être hyper réactifs », explique Laurent Maunoir. Une tendance accentuée par l’électrification des véhicules de Manitou, qui introduit de nouveaux composants dans les références de la BU, mais surtout par la forte croissance du groupe. Elle dépasse 20 % par an en moyenne depuis 2018 et s’élève à 26 % en 2022, avec un impact sur les volumes commandés de +8 à +10 %.
De plus en plus de commandes sur des pics horaires
En plus de l’augmentation mathématique des volumes à traiter, Manitou Spare Parts doit faire face à une nécessité de réactivité accrue pour répondre aux sollicitations urgentes de ses clients revendeurs, générant des pics de commande. « Quand ils reçoivent des machines à réparer, ils la diagnostiquent dans la journée, font le bilan de toutes les pièces de rechange qui vont permettre de les réparer et nous envoient leurs commandes en fin d’après-midi. Nous recevons donc de plus en plus de gros volumes de commandes sur une tranche horaire de plus en plus ramassée sur la fin de journée », explique Laurent Maunoir. L’entrepôt d’Ancenis livre aujourd’hui n’importe quel client dans le monde et expédie ses produits à 19 heures pour toute commande urgente passée le jour même avant 17 heures.
Nous avons construit ce projet de façon à pouvoir tenir au moins jusqu’en 2027
Avec cet équipement choisi pour sa capacité à s’adapter à la croissance du groupe, Laurent Maunoir estime avoir quelques années de gains de productivité devant lui. « Nous avons construit ce projet de façon à pouvoir tenir au moins jusqu’en 2027 », explique-t-il avant de préciser : « nous avons assez de surface au sol à côté de l’installation pour a minima rajouter une voire deux allées assez facilement ».
Le choix de Manitou de privilégier Mecalux a également été déterminé principalement par sa capacité à accompagner son client dans le déploiement du projet. « Nous avons axé la sélection sur la formation de notre maintenance, le SAV, l’accompagnement et les moyens mis sur le projet », confirme Laurent Maunoir.
Prise en main rapide et accompagnement du changement
L’outil de planification Synkron est déployé sur sept des huit entrepôts, le WMS Reflex (Hardis Group) est déployé sur trois entrepôts plus les Etats-Unis en cours de déploiement. La prise en main de la solution a en effet été rapide. Mecalux a travaillé à l’installation des racs au deuxième semestre 2021. Elle est opérationnelle depuis avril 2022, après trois mois de tests. S’en est suivi une rapide période de formation, apprentissage, calage et optimisation. « En une journée de formation, l’opérateur est efficace. La courbe du changement en termes de compétences et d’acceptation a été assez rapide », se félicite Laurent Maunoir.
Les équipes maintenance ont été formées, de nouveaux opérateurs ont été recrutés. Des changements s’appliquent également à l’organisation du travail. Des postes de conducteurs de ligne ont été créés par extension du périmètre de responsabilité de certains opérateurs et une plus grande rotation introduite sur les postes de picking. « Tenir la cadence sur ces postes demande de la vigilance. Pour garder de bonnes conditions de travail, nous estimons qu’il est plus efficace de faire tourner les effectifs sur ces types de poste plutôt que d’y fixer des titulaires », explique Laurent Maunoir.
Nous allons avoir beaucoup de données à notre disposition et beaucoup d’analyses possibles pour optimiser l’utilisation de l’outil
Après avoir fiabilisé le process, Laurent Maunoir entend maintenant aller plus loin dans la gestion de la productivité de l’outil et le traitement des pics d’activité, notamment. Pour ce faire, Manitou peut compter sur ses efforts préalables de digitalisation de la supply chain. L’outil de planification Synkron est déployé sur sept des huit entrepôts, le WMS Reflex (Hardis Group) est déployé sur trois entrepôts plus les Etats-Unis en cours de déploiement. « Nous allons avoir beaucoup de données à notre disposition et beaucoup d’analyses possibles pour optimiser l’utilisation de l’outil mais surtout le service qu’il rend au client », se projette Laurent Maunoir.